The Maximum Allowable Cycle Time Is Computed as
This feature presents several operational benefits. Solved Cycle time is not.
What Is The Difference Between Rpo Rto And Mtd Tandem
Daily operating time divided by the product of the desired output and the sum of job times.
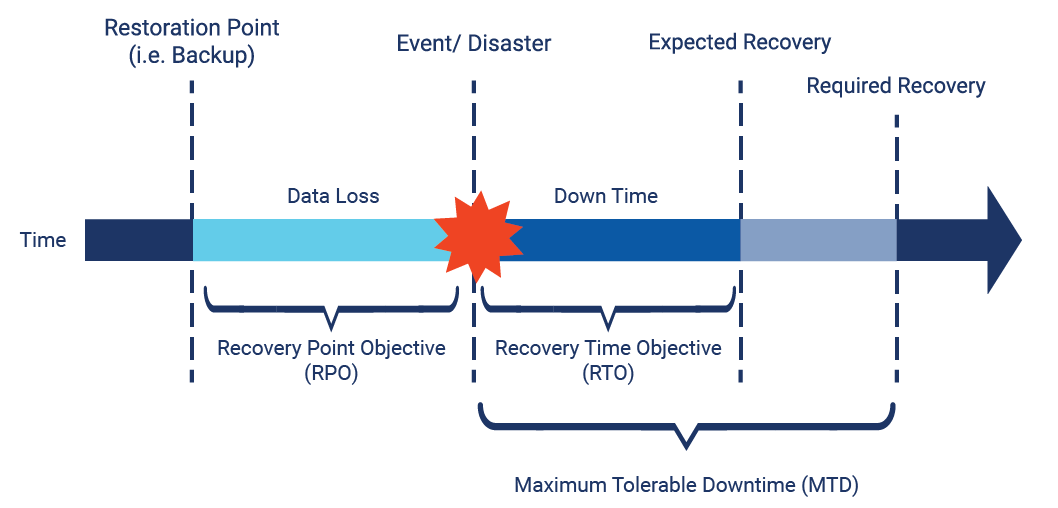
. Daily operating time divided by the desired output. In the vast majority of instances there will be numerous products or services being processed at any one time therefore the cycle time calculation needs to be modified as follows. Pump cycle time equals 60 minutes divided by the starts per hour so a maximum pump starts per hour of 6 equals a 10 minute cycle time.
Cycle time Tact time Effectively Daily Operating Time Required Daily Quantity of Ouptut. Downtime consists of two elements the systems recovery time and the work recovery time. They do not predict the cycle life of the vessel which normally will be larger.
The duty cycle can be used to define the ampacity of the charger. Desired output divided by the daily operating time C. Daily operating time divided by the desired output.
Adaily operating time divided by the desired output. This calculation is used to calculate. Time divided by units.
Currently with a Cycle Time of 1222 minutes youre running 222 minutes behind for each doll considering that your Cycle Time is longer than your Takt Time. Takt time is the maximum time within which all operations in the restaurant should be completed so as to meet their customer demand. Daily operating time divided by the product of the desired output and the sum of job times D.
The product of desired output and the sum of job times divided by daily operating time E. In this case the takt time is 6040 15 minutes. There is a correlation between the criticality of a business function and its maximum downtime.
Cdaily operating time divided by the product of the desired output and the sum of job times. The time required to complete a product from start to finish. THE MAXIMUM ALLOWABLE CYCLE TIME is a possible term which can describe the maximum Cycle time the engineers should design in to the system and it is usually set at 92-95 of Takt time Duggan 2002.
In the 2004 edition the equation for was also extended from a maximum of 2000000 cycles to an unlimited number of cycles. This is often known as Crew Size. In the document AB-516 ABSA defines maximum allowable working pressure MAWP as.
Throughput rate Units Produced or Tasks completed Time Cycle Time calculation in a Continuous Process. The maximum allowable time at each work station. Daily operating time divided by the product of desired output and the sum of job times 3.
Cycle Time 550 minutes 45 dolls 1222 minutesdoll. What are the minimum and maximum cycle times. Daily operating time divided by the product of the desired output and the sum of job times D.
VIII-2 fatigue methods calculate an allowable number of operating cycles with a factor of safety. Total Cycle TimeTAKT Time 1 This calculation demonstrates that you now need one workstation to complete this order of 24 forms in a day of 480 possible minutes working to a TAKT of 20 minutes. Desired output divided by the daily operating time C.
Daily operating time divided by the desired output B. The maximum allowable cycle time is computed as. How often items roll off the assembly line.
E100 minus station time. The effective daily operating time should not be reduced for any allowance due to machine breakdowns idle time awaiting materials rework or fatigue and rest time. The maximum allowable cycle time is computed as Adaily operating time divided by the desired output.
Takt time calculated by the formula available production time demand during that period. Maximum allowable cycle time in A Dictionary of Business and Management. The longest task is 24 minutes and the total time for all tasks is 18 minutes.
Desired output divided by the daily operating time. Cycle time is computed as _. Maximum Lead Pump Operating Range equals minimum cycle time multiplied by the Maximum Pumping Rate divided by 4.
The minimum value is 015 which results in an allowable displacement stress range for an indefinitely large number of cycles. The pressure authorized on the design registration or a lesser pressure as indicated on the manufacturers data report. Using these parameters the run quantity run time down time total production time and production rate partshr will be calculated.
Time divided by units. The maximum allowable cycle time is computed as. Dthe product of desired output and the sum of job times divided by daily operating time.
300 points Problem 6-1 An assembly line with 17 tasks is to be balanced. MAWP is measured at the top of the vessel. The charger can adjust itself to the maximum allowable current that can be delivered by various charging points for example a standard value of 16 A and a higher value of 32 A for semi-fast charging pointsThe standard value of 16 A will usually be the default value.
Recovery time objective RTO. 12 The equations found in ASME code books rarely provide real stresses that. Cycle Time Net Production TimeNumber of units made.
Further observations about this Cycle Time example. The lower Takt time is the larger the buffer needs to be to prevent being unable to deliver according to customer demand. The product of desired output and the sum of job times divided by daily operating time 4.
The formula for cycle time 1Throughput rate. Cycle time is not. Social sciences Business and Management.
MAWP is the highest pressure at which the equipment may be operated at its design temperature. The product of desired output and the sum of job times divided by daily operating time E. Daily operating time divided by the desired output B.
Round your answers to. The product of desired output and the sum of job times divided by daily operating time. The maximum time that can elapse between consecutive items leaving a production process if the designated capacity of the process is to be achieved.
The higher the criticality the shorter the MTD is likely to be. Operating time divided bu cycle time The maximum allowable cycle time is computed as. The maximum allowable cycle time is computed as.
Desired output divided by the daily operating time. Bdesired output divided by the daily operating time. Therefore MTD RTO WRT.
The line will operate for 450 minutes per day. Daily operating time divided by the product of the desired output and the sum of job times. Desired output divided by the daily operating time 2.
The production time for a manufacturing process is primarily determined from the cycle time but must also account for the defect rate machine uptime and machines used. The time available to recover disrupted systems and resources systems.
Pin By Jimy Kim On Electrical Engineering Articles In 2021 Power Engineering Electronic Engineering Electrical Inspection
No comments for "The Maximum Allowable Cycle Time Is Computed as"
Post a Comment